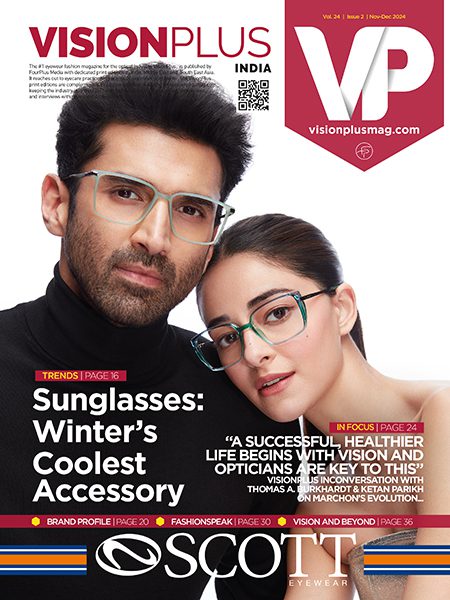
Six Sigma: Precision Tools For Optical Success
Adopting Japanese-inspired Six Sigma techniques, optical businesses can streamline processes and enhance customer experiences
This article explores Six Sigma, a crucial management tool that continues to play a pivotal role in reducing waste, enhancing operational efficiency and elevating customer satisfaction in the optical industry.
What Is Six Sigma?
At its core, Six Sigma is about reducing waste, minimising variability, and improving the quality of processes to meet customer expectations consistently. It’s a data-driven methodology that seeks to perfect outcomes by addressing inefficiencies in every step of a business operation.
Introduced by Bill Smith at Motorola in the 1980s, Six Sigma originated as a tool to increase organisational capability, optimise processes, and elevate employee morale while delivering superior products or services.
The principles were inspired by Japan's relentless commitment to quality, which transformed Motorola's television production line into a model of precision with negligible defect rates.
Fast forward to 2024, Six Sigma continues to thrive, adopted by leading companies like Amazon, American Express, Ford, General Motors, Infosys, Motorola, Reliance Industries and Tata Motors, with applications spanning manufacturing and service industries alike.
The Evolution of Six Sigma
Initially designed for manufacturing, Six Sigma now embraces service industries where the human element often dominates, for instance, in the optical business.
Six Sigma can focus on reducing customer complaints by standardising processes like frame fitting or lens customisation. Regardless of the industry, its success depends on clearly defined processes and measurable outcomes.
Today, Six Sigma is viewed in three distinct ways:
- As a Statistical Standard: Six Sigma equates to no more than 3.4 defects per million opportunities, ensuring near-perfection.
- As a Methodology: It provides a structured roadmap to problem-solving using tools like DMAIC (Define, Measure, Analyse, Improve, Control).
- As a Philosophy: It promotes continuous improvement by fostering customer-centric, data-driven decisions.
The Four Pillars of Six Sigma Success
Achieving Six Sigma requires alignment across four key aspects:
- Accuracy: Ensuring data reliability and completeness to eliminate errors.
- Cycle Time: Reducing delays in processes to increase efficiency.
- Cost: Controlling internal costs to deliver
maximum value. - Customer Satisfaction: The ultimate measure of success, reflecting a seamless experience.
The DMAIC Framework: A Roadmap to Excellence
The DMAIC process is a cornerstone of Six Sigma, offering a structured approach to problem-solving:
- Define:
- Identify customers and their expectations (Critical to Quality or CTQs).
- Map the process to pinpoint areas needing improvement.
- Establish clear project boundaries.
- Measure:
- Collect and analyse data to identify process defects or waste.
- Benchmark performance against customer expectations to locate gaps.
- Analyse:
- Examine data to uncover root causes of inefficiencies.
- Prioritise improvement opportunities based on their potential impact.
- Improve:
- Develop creative solutions to address inefficiencies.
- Implement plans that embed quality into the process.
- Control:
- Monitor the improved process to ensure sustainability.
- Document changes and institutionalise them through staff training, incentives, and system updates.
The Key Players in Six Sigma
Six Sigma projects involve multiple levels of expertise, each with specific roles:
- Black Belt: The project leader is trained in statistical tools and team management.
- Master Black Belt: A seasoned Black Belt who mentors others and oversees multiple projects.
- Green Belt: A part-time contributor to projects, trained in fundamental Six Sigma techniques.
- Process Owner: The individual responsible for the targeted process, ensuring sustained improvements.
Six Sigma in 2024: Broadening Horizons
Modern businesses operate in an era of heightened complexity, with digital transformation, sustainability and personalisation driving customer demands. Six Sigma has adapted to these shifts by integrating technologies like AI, machine learning and predictive analytics into its framework.
Even in service sectors such as hospitality or optical retail, Six Sigma principles are applied to streamline operations, from inventory management to customer engagement.
These industries leverage Six Sigma to reduce variability and maintain consistency, particularly as remote
work and digital interactions dominate customer interactions.
The Benefits of Six Sigma
The appeal of Six Sigma lies in its tangible benefits:
- Enhanced Quality: Fewer defects mean improved products and services.
- Cost Efficiency: Reducing waste directly impacts profitability.
- Employee Empowerment: Structured training builds skills and fosters a culture of accountability.
- Customer Loyalty: Consistently exceeding expectations strengthens trust and retention.
For instance, in an optical business, applying Six Sigma could mean aligning the sales process with customer needs by training staff to ask the right questions.
The Pursuit of Perfection
The ongoing significance of Six Sigma lies in its core philosophy: every process is measurable, and every outcome can be improved. It encourages working backwards—starting with a desired result and mapping the most effective path to achieve it.
In 2024, as optical businesses face evolving challenges, Six Sigma remains a cornerstone of operational excellence, adapting to diverse market needs and harnessing cutting-edge technology to break new ground. Its unwavering focus on perfection helps optical companies stay competitive, customer-centric, and efficient.
While perfection may be an elusive target, in striving for it, optical businesses achieve remarkable success.